Investigadores de la Universidad de Cambridge y la Universitat Politècnica de València (UPV) trabajan conjuntamente en un nuevo modelo de mejora funcional y estética a la hora de llevar la energía solar a la cerámica en el ámbito de la edificación. Se trata de una colaboración permanente entre investigadores del Institute for Manufacturing (IfM) de la Universidad de Cambrige (en concreto, Ronan Daly, Abir Al-Tabbaa, Regana Vasanthanayagam y María Cristina Rodríguez-Rivero), y Javier Orozco-Messana e Ian Fausto Zanchetta Chittka, de la Escuela Técnica Superior de Ingeniería de Edificación, Instituto de Tecnología de Materiales de la UPV.
Su objetivo final es la creación de baldosas fotovotlaicas con funcionalidad electrónica embebida por impresión superficial que ofrezcan nuevas posibilidades a la arquitectura.
Dos ventajas fundamentales
“La idea de tener aparatos electrónicos impresos en el exterior de los edificios no es nueva, pero integrarlos en baldosas cerámicas sí lo es, y creemos que ofrece dos ventajas fundamentales”, afirma Daly. “La primera es que alarga la vida útil de los dispositivos electrónicos”, indica el investigador del IfM. “Los componentes electrónicos externos, especialmente los orgánicos, se degradan rápidamente a medida que se exponen a los elementos. Al incrustar las conexiones y los dispositivos eléctricos dentro de la baldosa, muchas de estas partes podrían protegerse con aquellas funciones no embebibles interconectadas con la baldosa a voluntad”, dice.
Y prosigue: “La segunda ventaja es que se trata de un proceso que la industria de las baldosas cerámicas ya está preparada para implementar. En países productores tradicionales como España e Italia se ha producido un cambio en toda la industria de la serigrafía convencional de gráficos, con tiradas grandes de impresión por inyección de tinta e impresión bajo demanda. Ello ha reducido significativamente tanto el desperdicio como el almacenamiento, y ha ayudado a estos fabricantes a competir con nuevos productores como China”.
Desafíos de la investigación
Actualmente, los investigadores están desarrollando un sistema que preserva la funcionalidad de la electrónica embebida a través de un proceso que permite soportar tanto los elevados esfuerzos mecánicos presentes durante el prensado como las temperaturas extremas de cocción, permitiendo la integración total de la funcionalización electrónica en el proceso industrial de fabricación de baldosas.
La materia prima de la baldosa se reduce a una mezcla de polvo cerámico que, tras su prensado, es cocida a 1200° C, por lo que crear componentes electrónicos que puedan sobrevivir a tales temperaturas supone un desafío. Para superarlo, se pretende controlar la cantidad de oxígeno presente durante el proceso, algo que a día de hoy es viable en laboratorios, pero no es práctico para uso industrial.
A su vez, el equipo trabaja en el control de la porosidad de la cerámica, ya que se necesita espacio dentro de la baldosa para poder acumular la energía eléctrica generada fotovoltaicamente para alimentar los distintos circuitos electrónicos.
“Existe un método para incrustar componentes electrónicos que utiliza la compresión en dos etapas, que ya se utiliza en baldosas cerámicas”, señala Daly. “Nuestra alternativa radica en imprimir los elementos con tintas especiales entre las distintas capas de compresión”, explica el investigador.
El control de la porosidad permite embeber grafeno dentro de la amplia superficie de la porosidad conectada. Este, tras un tratamiento termoquímico adecuado, se convierte en un súper condensador que acumula o distribuye la energía fotovoltaica, a través de contactos internos, a los componentes incrustados, perfectamente seguros entre las dos capas cerámicas.
“Ahora”, continúa Daly, “estamos estudiando los detalles del flujo poroso y la sinterización del material para comprender cómo controlar mejor este proceso. Cuando se refine este proceso, los nuevos mosaicos funcionales se podrán producir a gran escala, combinando funcionalidades electrónicas elementales que puedan simultáneamente generar energía y utilizarla mientras desarrollan su trabajo, potenciando su efecto sinérgico conectándose entre sí para asumir funciones complejas dentro del edificio”.
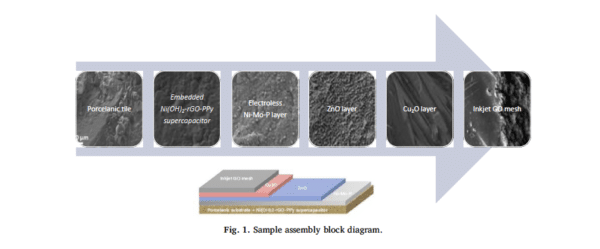
Célula solar de HTJ
En el artículo “Cu2O–ZnO heterojunction solar cell coupled to a Ni(OH)2-rGO-PPy supercapacitor within a porous stoneware tile”, publicado en Ceramics International, el equipo obtuvo los primeros resultados experimentales.
Partiendo de una baldosa de gres porosa, una capa conductora de Ni-Mo-P sin electrodos es el punto de partida para infiltrar en la porosidad conectada (estructura libre 3D) del espesor de la baldosa un compuesto de Ni(OH)2-rGO-PPy nanoestructurado que actúa como supercondensador. En la superficie conductora abierta se cultivó una heterounión (HTJ) optimizada de p-Cu2O/n-ZnO que integraba un circuito eléctrico acoplado de almacenamiento de carga sin fisuras en una baldosa comercial.
La capa conductora elegida se ha obtenido por deposición electrolítica. “Dentro del abanico de capas posibles, el Ni-Mo-P muestra el perfil más atractivo, no solo por sus propiedades eléctricas (conductividad y alineación de niveles de energía) sino que además es un proceso de bajo coste, fácil de aplicar y escalable que permite la deposición de recubrimientos homogéneos de aleación con espesor uniforme sobre una superficie no conductora”, explica el equipo.
Una vez electrodepositada la capa de ZnO sobre el sustrato cerámico metálico, se electrodepositó la capa de Cu2O para obtener una célula solar de tipo heterounión p-n. La capa de Cu2O se sintetizó utilizando una célula convencional de tres electrodos, en la que se utilizó la capa de ZnO anterior sobre la cerámica como electrodo de trabajo, un hilo de platino como contraelectrodo y un Ag/AgCl como electrodo de referencia.
Partiendo de una preparación no estándar del porcelánico, la porosidad generada permitió la integración en la superficie interna de los poros conectados de un dispositivo supercapacitor asimétrico Ni(OH)2/rGO/ PPy. Este supercondensador presenta una excelente densidad energética de 26′3 Wh/kg y una densidad de potencia de 2,918 kW/kg.
En la superficie externa se optimizó un recubrimiento metálico de Ni-Mo-P sin electrodos para que funcionara como contacto posterior de una célula solar electrodepositada.
“El supercondensador ensamblado se acopla así a una célula solar de heterounión Cu2O/ ZnO de bajo coste que ha sido probada para generar energía con una eficiencia razonable. Sin embargo, el mayor logro ha sido la fabricación de una unidad autónoma autosostenible integrada en una baldosa de fachada comercial”, dicen los investigadores.
Desarrollo de prototipos preindustriales
Como parte del proceso, el equipo investigador trabaja ya en el desarrollo de prototipos industriales, como indica, Javier Orozco, investigador de la UPV: “Tras los prometedores resultados obtenidos, estamos ya trabajando con una empresa en el desarrollo de prototipos preindustriales para su utilización en pilotos”.
“Esperamos desarrollar la patente de concepto que ya está registrada, y tener una implantación real, vinculada a un proyecto de la última convocatoria del Green Deal de la Unión Europea, en Lovaina, Frankfurt-am-Oder, Udine y Valencia, para avanzar en el desarrollo de las nuevas ciudades verdes y sostenibles”, concluye.
La energía generada no afectaría al aspecto exterior del edificio, por lo que facilitaría la opción de adaptar medioambientalmente edificios históricos, llegando a lugares donde habitualmente los paneles solares no son apropiados, y permitiendo dotar de un carácter más ecológico a elementos patrimoniales sin que estos pierdan su carácter protegido.
Este contenido está protegido por derechos de autor y no se puede reutilizar. Si desea cooperar con nosotros y desea reutilizar parte de nuestro contenido, contacte: editors@pv-magazine.com.
Al enviar este formulario, usted acepta que pv magazine utilice sus datos con el fin de publicar su comentario.
Sus datos personales solo se divulgarán o transmitirán a terceros para evitar el filtrado de spam o si es necesario para el mantenimiento técnico del sitio web. Cualquier otra transferencia a terceros no tendrá lugar a menos que esté justificada sobre la base de las regulaciones de protección de datos aplicables o si pv magazine está legalmente obligado a hacerlo.
Puede revocar este consentimiento en cualquier momento con efecto para el futuro, en cuyo caso sus datos personales se eliminarán inmediatamente. De lo contrario, sus datos serán eliminados cuando pv magazine haya procesado su solicitud o si se ha cumplido el propósito del almacenamiento de datos.
Puede encontrar más información sobre privacidad de datos en nuestra Política de protección de datos.